Plasma cutting technology has revolutionized metal fabrication, offering precision, speed, and versatility that traditional cutting methods struggle to match. Whether you’re a hobbyist, a small workshop owner, or an industrial manufacturer, understanding the latest advancements in plasma cutting can significantly enhance your workflow. In this comprehensive guide, we will explore three critical aspects of modern plasma cutting: PlasmaSens, THC plasma cutters, and Mach3 plasma setup.
PlasmaSens represents the next generation of sensor technology, optimizing cut quality and machine longevity. Meanwhile, THC plasma cutters (Torch Height Control systems) ensure consistent arc distance, reducing errors and material waste. Finally, integrating a Mach3 plasma setup allows for seamless CNC control, bridging the gap between manual operations and automated precision.
Each of these components plays a vital role in maximizing efficiency and accuracy in plasma cutting. By the end of this article, you will have a deeper understanding of how PlasmaSens, THC plasma cutters, and Mach3 plasma setup work together to deliver superior cutting performance. Whether you’re troubleshooting an existing system or planning an upgrade, this guide will provide the insights you need to make informed decisions. Let’s dive into the details of these cutting-edge technologies.
What Is PlasmaSens and How Does It Enhance Plasma Cutting?
Plasma cutting relies on precision, and even minor inconsistencies in arc voltage or torch height can lead to poor cut quality, excessive dross, or premature consumable wear. This is where PlasmaSens technology comes into play—a sophisticated sensing system designed to optimize plasma cutting performance by monitoring and adjusting critical parameters in real time.
PlasmaSens works by continuously measuring arc voltage and other electrical signals during the cutting process. This data is then processed to make instantaneous adjustments, ensuring optimal torch height and arc stability. Unlike traditional systems that rely on preset values, PlasmaSens dynamically adapts to variations in material thickness, surface conditions, and even minor fluctuations in power supply. The result is cleaner cuts, reduced consumable wear, and greater overall efficiency.
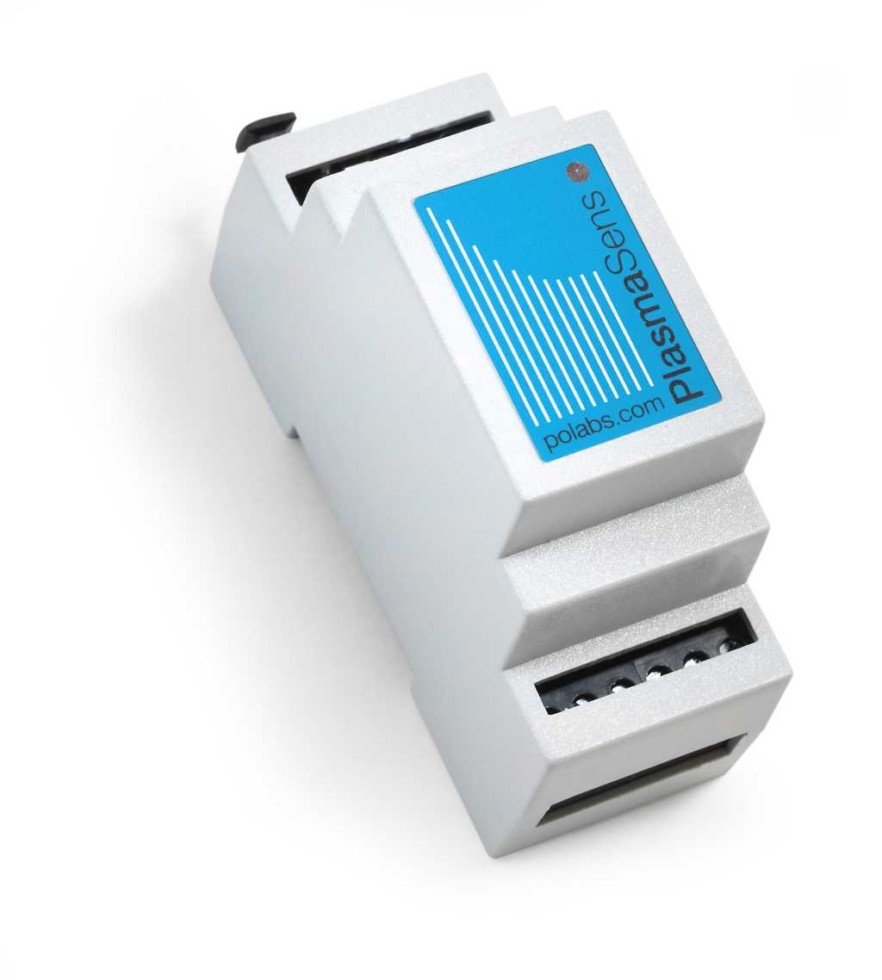
One of the key advantages of PlasmaSens is its ability to compensate for warped or uneven materials. In conventional setups, an inconsistent surface can cause the torch to either drag or lift too high, leading to poor cut quality. With PlasmaSens, the system detects these irregularities and automatically adjusts the torch height, maintaining the ideal arc gap throughout the cut. This is particularly beneficial when working with reclaimed or imperfect metal sheets, where manual adjustments would be impractical.
Another critical feature of PlasmaSens is its role in prolonging consumable life. By maintaining precise arc voltage and minimizing unnecessary torch collisions, the system reduces wear on nozzles, electrodes, and shields. This not only lowers operating costs but also minimizes downtime for consumable replacement. For high-production environments, where even minor delays can impact productivity, PlasmaSens offers a significant advantage.
Integration with modern CNC plasma systems further enhances the capabilities of PlasmaSens. When paired with advanced controllers, the sensor data can be used to fine-tune cutting paths, adjust feed rates, and even predict potential issues before they occur. This level of automation is particularly valuable in industrial settings, where repeatability and efficiency are paramount.
In summary, PlasmaSens represents a major leap forward in plasma cutting technology. By providing real-time feedback and adaptive control, it addresses some of the most common challenges in plasma cutting—material inconsistencies, consumable wear, and arc stability. Whether you’re running a small fabrication shop or a large-scale manufacturing operation, incorporating PlasmaSens into your setup can lead to noticeable improvements in cut quality, cost savings, and overall productivity. As plasma cutting continues to evolve, technologies like PlasmaSens will play an increasingly vital role in shaping the future of metal fabrication.
How Does a THC Plasma Cutter Improve Cutting Precision?
Precision is the cornerstone of effective plasma cutting, and maintaining the correct torch-to-workpiece distance is critical for achieving clean, consistent cuts. This is where THC plasma cutter (Torch Height Control) technology proves indispensable. A THC plasma cutter automatically adjusts the height of the plasma torch during operation, compensating for material warping, uneven surfaces, and thermal distortion. But how exactly does it work, and why is it such a game-changer for both hobbyists and industrial users?
At its core, a THC plasma cutter relies on real-time voltage monitoring to determine the optimal arc length. The system continuously measures the voltage between the torch and the workpiece, using this data to raise or lower the torch as needed. If the voltage rises—indicating the torch is too far from the material—the THC plasma cutter lowers the torch to maintain proper arc energy. Conversely, if the voltage drops (signaling the torch is too close), the system retracts it to prevent collisions and nozzle damage. This dynamic adjustment ensures consistent cut quality, even when working with imperfect or heat-warped metal.
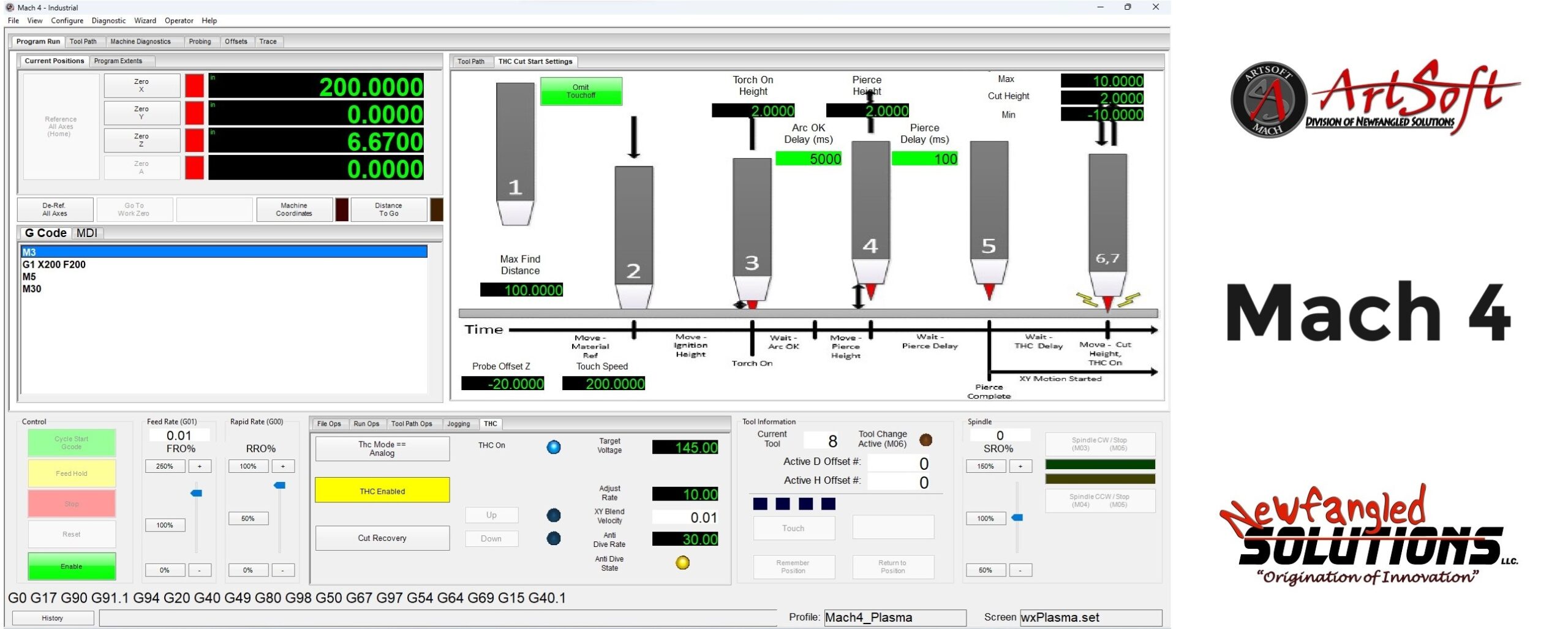
One of the most significant advantages of a THC plasma cutter is its ability to handle bevel cuts and intricate shapes without manual intervention. Traditional plasma cutting often requires constant operator adjustments when dealing with angled or contoured edges, leading to inconsistencies. With a THC plasma cutter, the system automatically compensates for these variations, maintaining the correct standoff distance throughout the entire cut. This is especially valuable in applications like automotive fabrication, shipbuilding, and artistic metalwork, where precision is non-negotiable.
Another key benefit is the reduction in consumable wear. When a plasma torch operates too close to the material, it risks damaging the nozzle and electrode, leading to frequent replacements. On the other hand, excessive distance can cause poor cut quality and excessive slag. A THC plasma cutter eliminates these issues by maintaining the ideal arc gap, extending consumable life and reducing operational costs. For businesses running high-volume production, this translates to fewer interruptions and higher profitability.
Integration with CNC systems further enhances the capabilities of a THC plasma cutter. Advanced controllers can use THC data to optimize feed rates, adjust for piercing delays, and even predict material behavior based on previous cuts. Some modern systems also incorporate collision detection, where the THC can perform emergency retractions if an unexpected obstruction is detected. This level of automation is particularly beneficial in industrial environments, where efficiency and repeatability are crucial.
In conclusion, a THC plasma cutter is more than just a convenience—it’s a necessity for anyone serious about plasma cutting. By automating torch height adjustments, it ensures cleaner cuts, longer consumable life, and greater efficiency across a wide range of applications. Whether you’re a DIY enthusiast working on small projects or a professional fabricator handling large-scale production, incorporating a THC plasma cutter into your setup will elevate your results and streamline your workflow. As plasma technology continues to advance, THC systems will remain a fundamental component in achieving precision and reliability.
What Is a Mach3 Plasma Setup and How Does It Optimize CNC Cutting?
For CNC plasma cutting enthusiasts and professionals alike, software control is just as crucial as hardware performance. Among the most widely used solutions is the Mach3 plasma setup, a powerful and versatile CNC control system that brings precision, customization, and automation to plasma cutting operations. But what exactly makes Mach3 plasma setup so effective, and how does it enhance the overall cutting process?
At its foundation, Mach3 plasma setup is a software-based CNC controller that transforms a standard computer into a fully functional machine control unit. Designed to operate with a variety of plasma cutters, Mach3 plasma setup provides users with intuitive G-code interpretation, real-time toolpath adjustments, and extensive customization options. Unlike proprietary CNC systems that lock users into rigid workflows, Mach3 plasma setup offers flexibility, making it ideal for hobbyists, small shops, and even industrial applications where adaptability is key.
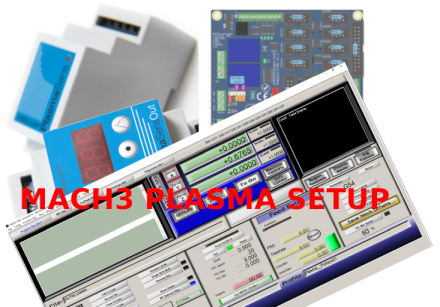
One of the standout features of a Mach3 plasma setup is its ability to integrate seamlessly with THC (Torch Height Control) systems. By synchronizing with a THC module, Mach3 plasma setup dynamically adjusts the torch height during cutting, compensating for material inconsistencies and thermal distortion. This ensures consistent arc distance, which directly translates to cleaner cuts, reduced dross, and extended consumable life. The software’s real-time monitoring capabilities also allow for immediate corrections, minimizing errors before they affect cut quality.
Another advantage of Mach3 plasma setup is its support for custom macros and scripting. Advanced users can program specific cutting routines, automate repetitive tasks, or even create specialized functions for unique projects. For example, a fabricator working with varying material thicknesses can write a script that automatically adjusts feed rates and plasma power settings based on the G-code instructions. This level of automation not only saves time but also reduces the likelihood of human error, particularly in complex or high-precision jobs.
Additionally, Mach3 plasma setup excels in its compatibility with a wide range of hardware. Whether using stepper or servo motors, different plasma cutter brands, or third-party sensors, the software can be configured to work harmoniously with nearly any setup. This makes it an excellent choice for retrofitting older machines or building custom CNC plasma tables from scratch. The ability to fine-tune motor tuning, acceleration, and backlash compensation further ensures smooth and precise motion control, which is critical for intricate designs and high-speed cutting.
Despite its many strengths, a Mach3 plasma setup does require some technical knowledge to fully leverage its capabilities. Users must familiarize themselves with G-code programming, machine calibration, and parameter adjustments to achieve optimal results. However, the active user community and abundance of online resources make the learning curve manageable, even for beginners.
In summary, a Mach3 plasma setup is a powerful, adaptable, and cost-effective solution for CNC plasma cutting. By combining precise motion control, real-time THC integration, and extensive customization options, it empowers users to achieve professional-grade results without the constraints of closed-loop systems. Whether you’re building a DIY plasma table or optimizing an existing setup, implementing Mach3 plasma setup can significantly enhance accuracy, efficiency, and overall cutting performance. As CNC technology evolves, Mach3 remains a trusted platform for those who demand both control and versatility in their plasma cutting operations.
Elevating Plasma Cutting with PlasmaSens, THC, and Mach3
Plasma cutting technology has come a long way from its early days of manual operation and inconsistent results. Today, advancements like PlasmaSens, THC plasma cutters, and Mach3 plasma setup have transformed the industry, offering unprecedented precision, efficiency, and automation. Together, these technologies address the most common challenges in metal fabrication—ensuring clean cuts, reducing waste, and optimizing workflow—whether for hobbyists, small shops, or large-scale industrial operations.
PlasmaSens has redefined how plasma cutters interact with materials by introducing real-time adaptive control. By continuously monitoring arc voltage and adjusting torch height dynamically, it eliminates guesswork and compensates for imperfections in metal surfaces. This not only improves cut quality but also extends the lifespan of consumables, making it a cost-effective upgrade for any serious fabricator.
Meanwhile, THC plasma cutters have become indispensable for maintaining consistent arc distance, especially when dealing with warped or uneven materials. The ability to automatically adjust torch height during complex cuts—such as bevels or intricate contours—ensures precision without requiring constant manual intervention. For businesses looking to minimize downtime and maximize output, integrating a THC plasma cutter is a logical step toward greater productivity.
Finally, the Mach3 plasma setup bridges the gap between hardware and software, offering a customizable CNC control solution that adapts to diverse cutting needs. Its compatibility with various hardware components, support for scripting and macros, and seamless THC integration make it a versatile choice for both DIY builders and professional fabricators. While it demands some technical know-how, the payoff in precision and automation is well worth the effort.
As the demand for faster, smarter, and more reliable plasma cutting grows, technologies like PlasmaSens, THC plasma cutters, and Mach3 plasma setup will continue to play pivotal roles. Whether you’re upgrading an existing system or building a new one from scratch, incorporating these innovations will future-proof your operations and elevate your results. The future of plasma cutting is here—and it’s sharper, smarter, and more efficient than ever.